预制直埋保温管是由钢管、玻璃钢内护套、玻璃钢外壳构成,其特征是:还包括耐高温绝热保温层、润滑层、弹性密封件。本实用新型有效的解决了城镇集中供热中130℃-600℃高温输热用预制直埋保温管的保温、滑动润滑和裸露管端的防水问题。
预制直埋保温管不仅具有传统地沟和架空敷设管道难以比拟的先进技术、实用性能,而且还具有显著的社会效益和经济效益,也是供热节能的有力措施。预制直埋保温管采用直埋供热管道技术,标志着中国供热管道技术发展已经进入了新的起点。
预制直埋保温管主要由四部分组成:
(1)工作钢管:根据输送介质的技术要求分别采用有缝钢管、无缝钢管、双面埋弧螺旋焊接钢管。
(2)保温层:采用硬质聚氨酯泡沫塑料。
(3)保护壳:采用高密度聚乙烯或玻璃钢。
(4)渗漏报警线:制造高温预制直埋保温管时,在靠近钢管的保温层中,埋设有报警线,一旦管道某处发生渗漏,通过警报线的传导,便可在专用检测仪表上报警并显示出漏水的准确位置和渗漏程度的大小,以便通知检修人员迅速处理漏水的管段,保证热网安全运行。
预制直埋保温管优势特点:
1 降低工程造价。
据有关部门测算,双管制供热管道,一般情况下可以降低工程造价的25%(采用玻璃钢做保护层)和10%(采用高密度聚乙烯做保护层)左右。
2 热损耗低,节约能源。
预制直埋保温管其导热系数为:λ=0.013—0.03kcal/m·h·oC,比其他过去常用的管道保温材料低得多,保温效果提高4~9倍。再有其吸水率很低,约为0.2kg/m2。吸水率低的原因是由于聚氨酯泡沫的闭孔率高达92%左右。低导热系数和低吸水率,加上保温层和外面防水性能好的高密度聚乙烯或玻璃钢保护壳,改变了传统地沟敷设供热管道“穿湿棉袄"的状况,大大减少了供热管道的整体热损耗,热网热损失为2%,小于国际10%的标准要求。
3 防腐,绝缘性能好,使用寿命长。
预制直埋保温管由于聚氨酯硬质泡沫保温层紧密地粘结在钢管外皮,隔绝了空气和水的渗入,能起到良好的防腐作用。同时它的发泡孔都是闭合的,吸水性很小。高密度聚乙烯外壳、玻璃钢外壳均具有良好的防腐、绝缘和机械性能。因此,工作钢管外皮很难受到外界空气和水的侵蚀。只要管道内部水质处理好,据国外资料介绍,预制直埋保温管的使用寿命可达50年以上,比传统的地沟敷设、架空敷设使用寿命高3~4倍。
4.占地少,施工快,有利环境保护。
预制直埋保温管不需要砌筑庞大的地沟,只需将保温管埋人地下,因此大大减少了工程占地,减少土方开挖量约50%以上,减少土建砌筑和混凝土量90%。同时,保温管加工和现场挖沟平行进行,只需现场接头,可以缩短工期约50%以上。
5 安全。
除中国外生产的预制直埋保温管,均设有渗漏报警线,一旦管道某处发生渗漏,通过报警线的传导,便可在专用检测仪表上显示出保温管道渗水、漏水的准确位置及渗漏程度的大小,以便通知检渗人员迅速处理漏水的管段,保证供热管网的安全运行。国内生产的保温管目前末设渗漏报警线,有待补上这一空白。
总之,预制直埋保温管不仅具有传统地沟和架空敷设管道难以比拟的先进技术、实用性能,而且还具有显著的社会效益和经济效益,也是供热节能的有力措施。采用直埋供热管道技术,标志着中国供热管道技术发展已经进入了新的起点。随着这项先进技术的进一步完善和发展,供热管道直埋取代地沟和架空势在必行。
预制直埋保温管广泛用于液体、气体的输送管网, 化工管道保温工程石油、化工、集中供热热网、中央空调通风管道、市政工程等。
预制保温管是由高密度聚乙烯外护管、聚氨酯硬质泡沫塑料保温层和钢管组成,三者结合为一个紧密的整体。由于三者成为一体直埋于土壤中,内管温度变化引起的热胀应力通过聚氨酯保温层传递给外护管,外护管受到的土壤摩擦力也是通过聚氨酯保温层传递给钢管,这就要求聚氨酯除具有保温功能外,还必须具有一定的抗压和抗剪切强度。本公司采用进口聚氨酯原料,能够承受 130 ℃ 的连续工作温度,满足抗压和抗剪切强度。为进一步保证直埋管的一体性,对工作钢管外表面进行抛丸处理,对外护管内表面进行电晕处理,以增强聚氨酯与这两个表面的粘合力。
我公司生产的直埋保温管符合国家行业标准 CJ/T114-2000 《 高密度聚乙烯外护管聚氨酯泡沫塑料预制保温管》和欧洲标准 EN253 《用于地下热水管网的整体式预制保温管系统一由工作钢管、聚氨酯保温层和聚乙烯外护管组成的保温管》
直埋保温管适用于输送连续工作温度不高于 130 ℃ ,工作压力不大于 2.5MPa 的各类介质,如采暖热水、中央空调用冷热水、高粘度的原油和重油等。
根据用户的具体要求,内工作管也可以选用高密度聚乙烯管、不锈钢管或铜管。本设计手册按照内工作钢管为 20 号钢的无缝钢管(GB/T8163 - 1999 或 GB3087 - 1999 ) 编制。
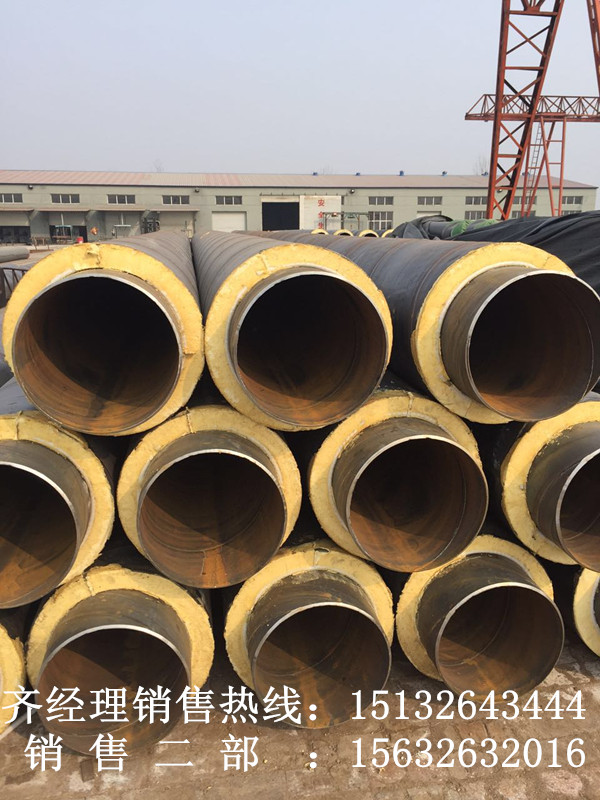
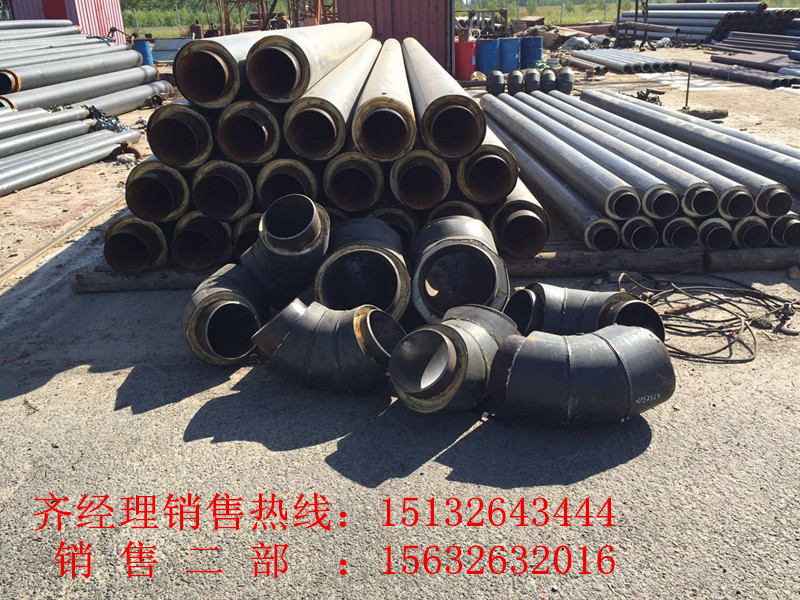

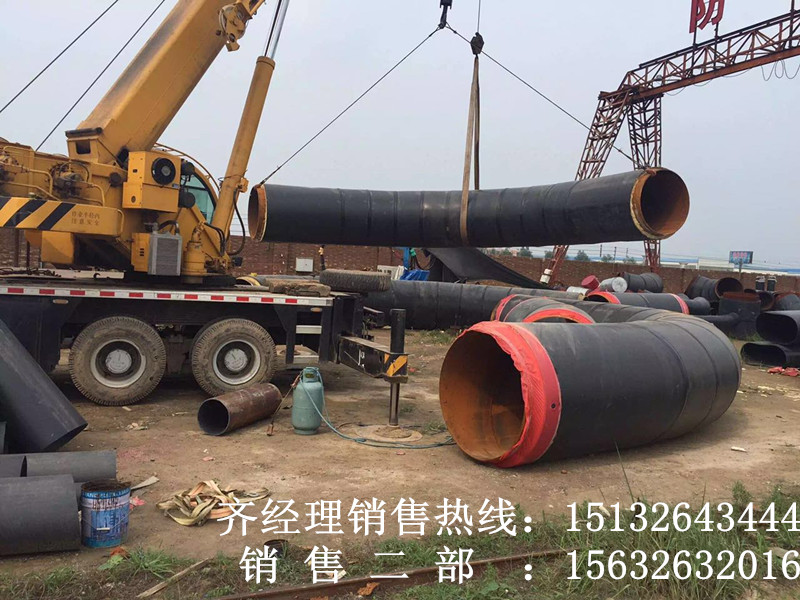