详细介绍: 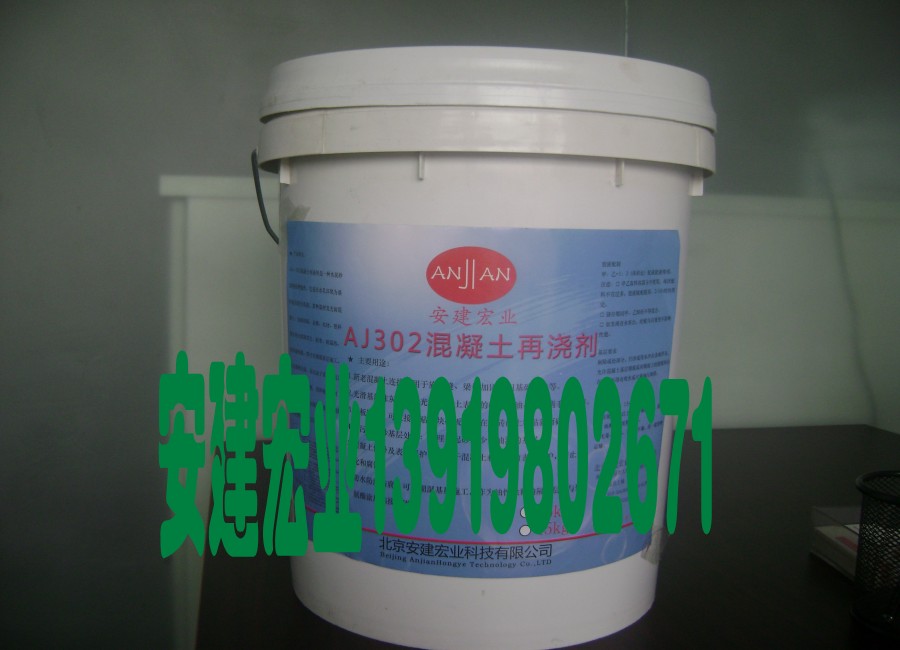
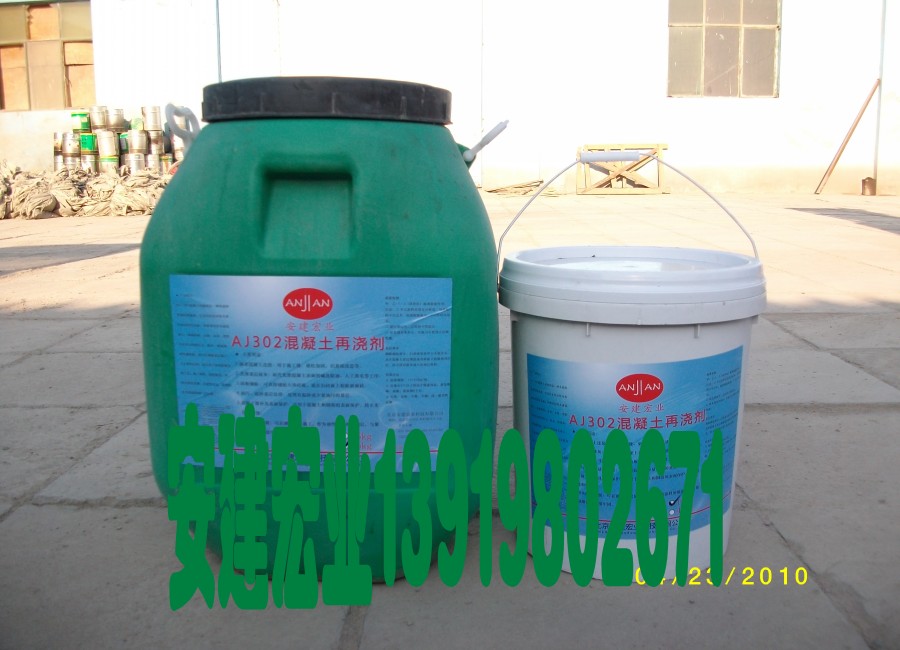
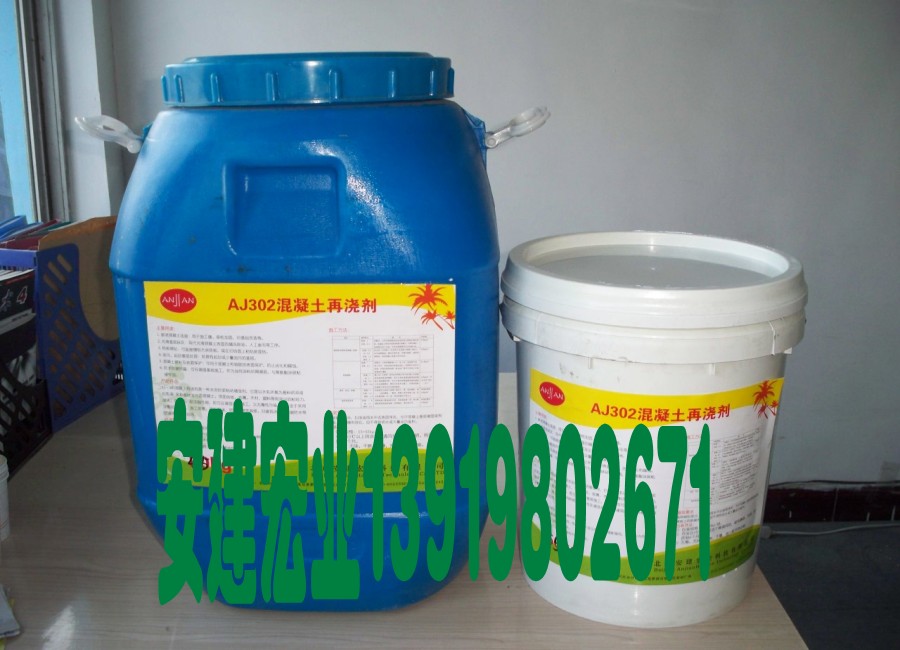
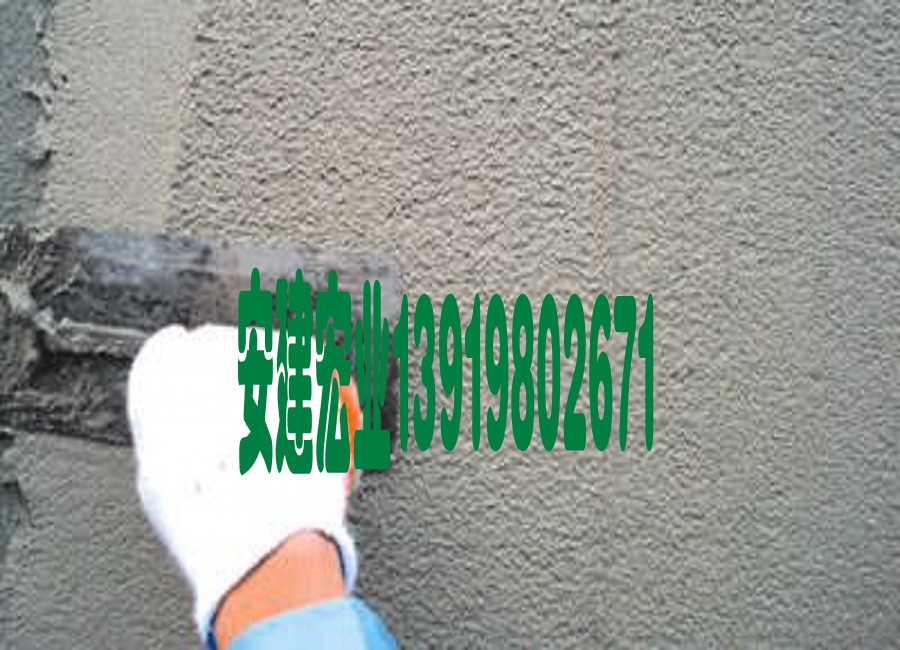
西宁混凝土界面剂施工条件 13919802671李经理
1 、胶液配制甲组分:乙组分 =1 : 3( 体积比 ) 配成胶液待用。
注意: (1) 甲、乙取料容器分开使用,每次配料不宜过多,胶液随配随用, 3h 内用完。 (2) 贮存期间甲、乙组分不得混合,贮存温度不得低于 5 ℃ ,贮存期半年至一年。 (3) 如发现甲组分有水析出,经搅拌均匀后使用不影响性能。
2 、基层要求
剔除混凝土上基层表面的疏松部分,扫净或用水冲去表面浮灰,允许混凝土基层潮湿或有模板上的脱模剂存在,但不得有明水或大量油污堆集。
3 、施工方法
使用部分
|
填料配比
|
作 用
|
用胶量
|
基层抹灰
新老砼连接
|
胶液: 1
水泥: 0 ~ 1
|
涂敷法 ( 趁湿抹灰 )
1 、用毛刷将配好的处理剂均匀地涂刷在基层表面。
2 、趁其未干立即抹水泥砂浆或打混凝土。
3 、夏季施工时,如处理剂涂刷后表干太快,则可用水浸湿基层,然后涂刷处理剂。
|
0.2kg /m 2
|
胶液: 0.5
水: 0.5
水泥: 1.5
黄砂: 2
|
拉毛法 ( 干后抹灰 )
1 、接比例配成稀砂浆。
2 、用刷子、扫帚等工具甩刷于混凝土基层上,拉毛成粗糙面,等硬化后再抹灰。
3 、遇有模板,钢筋障碍处,新老砼连接可采用此法。
|
0.3kg /m 2
|
砖板铺地
|
胶液: 1
水泥: 0 ~ 1
|
涂敷法 ( 趁湿抹灰 )
1 、面砖铺贴施工中,除了加一道涂刷 302 的工序外,其它均按传统作法进行。
2 、面砖不必用水浸泡。
3 、在要进行粘贴的面砖背面涂刷一道处理剂,然后立即抹上水泥砂浆进行铺贴。
|
0.2kg /m 2
|
|
胶液: 1
水: 1
水泥: 2 ~ 4
黄砂: 4 ~ 6
|
掺入法
1 、面砖、花岗石等砖板可刚稀释后的 302 掺入水泥细砂拌成砂浆直接铺贴。
2 、在旧瓷砖或聚氨酯等涂料墙面上直接铺新面砖时,先按上面的“拉毛法”在旧瓷砖或涂料墙面上拉毛成粗糙面,待硬化后再按本掺入法拌成砂浆铺贴。
注意旧瓷砖或涂料墙面不得有松动空鼓和脱皮。
|
0.5kg /m 2
( 以结合层 3mm 计 )
|
砼表面保护
防水防潮处理
|
胶液: 1
水泥: 1 ~ 2
细砂: 1 ~ 2
|
配制成稀或稠浆,均匀涂刷于清理干净的砼基层上,第一道用稀浆,第二、三道用稠浆,砼保护涂刷二道,防水、防潮需刷二至三道,每道间隔 4h 以上 ( 等上一道干后 )
|
每道用量
0.2kg /m 2
|
起砂地面处理
|
胶液: 1
水泥: 1 ~ 2
细砂: 1 ~ 2
|
清除地面已脱落疏松灰砂,用胶液先涂刷一道,然后配制砂浆刮涂起砂地面一至两遍后,洒水泥压光。
|
每道用量
0.2kg /m 2 左右
|
五、 302 界面处理剂能够处理以下病症
1 、混凝土表面“起砂”
混凝土施工完毕,经过一段时间的养护(混凝土胶结凝固)后,发现砼的表面一层不具强度而“起砂”,砼的耐磨性、耐久性及抗渗性会下降。产生此类现象有以下原因:
a )混凝土配料不当。如水灰比相对过大、灰砂比过小、砂率及细集料量过高、减水剂及缓凝剂等外加剂过多等,致使砼的强度过低。 b )水泥质量的影响。主要表现有强度太低、安定性不合格、凝结时间过长、比表面积过小(细度过粗)、颗粒级配过分集中、碱性及非活性混合材料占水泥组分的比例过大等因素,将造成混凝土水化凝结较慢、泌水性较大,从而导致砼的表面强度过低。 c )其他组成材料的影响。如砂石不干净(泥含量较大)、砂的细度模数过高或过低等,也会使混凝土强度降低、泌水性增加。 d )混凝土施工不当。振捣过度,造成砼严重析水;二次抹面不当或没有进行抹面,抹面时间过早(未到初凝)或过晚(终凝以后),抹面时发现析出水较多而另加过量的水泥补面等都有可能造成混凝土表面起砂。 e )成型养护不当。湿养护过度,如在砼表面硬化前被大水冲刷;湿养护不足,砼内水分蒸发散失;湿养护过早,成型后未到初凝即过早浇水等。 f )环境因素的影响。如施工环境空气中 CO 2 浓度较高,与水泥凝胶中的 Ca(OH) 2 作用后使其表面碱度降低导致硬化不良;已经硬化的砂浆和混凝土在未达到一定强度之前经常受到曝晒、风吹、雨淋、干湿循环或碳化作用等等。
2 、混凝土表面“脱皮”
混凝土成型几天后,表面薄薄的一层呈块状脱落,紧挨脱皮的底层通常还会有“起砂”的现象。能引“起砂”的因素都有可能造成脱皮,另外还要注意以下几点:
a )温度的影响。如养护用水太冷( < 10 ℃ )或太热( > 60 ℃ ),使养护温度与混凝土水化温差太大;在施工浇注初期气温突降或遇霜冻、雾浸等。 b )抹面操作不当。如抹面过早、抹面次数过多、抹面用力过度或集中重复抹面等。 c )水泥及集料中碱含量、碳含量等危害元素超标。
3 、混凝土不“收旱”
混凝土施工到达一定时间后,强度低,表现出浆体粗糙、松散、凝结不好或强度不够。主要原因有:
a )施工过程的问题。包括混凝土配比设计、拌和、成型、浇注、养护、保养等操作不当,导致混凝土标号低劣,强度不够。 b )所用材料不合格。如砂、石、集料质量不合格;除此之外,大多数是因为水泥体积膨胀率太大(安定性严重不良)。 c )施工用木质模板未经水浸,其内壁大量吸附砼内水份,导致砼体严重缺水而降低强度。 d )水泥水化硬化缓慢,强度等级太低,标号不够;或者水泥出现急凝或假凝,使水泥强度不能有效发挥。
4 、混凝土“开裂”
混凝土出现裂纹或裂缝,通常有以下原因: a )配制混凝土时水灰比过小、灰砂比过大、砂率较小、或外加剂过多,使混凝土水化用水相对不足,形成“刚性材料”,经养护后,砼内部在热应力作用下结构发生膨胀而“开裂”。 b )所用骨料粒径过大,在水灰比大的情况下极易形成空洞,水分蒸发时会产生“裂纹”;并且因混凝土表层水泥不能得到完全水化,当底层强度发挥后,其应力大于表层产生的应力,从而出现“开裂”。 c )搅拌不匀、养护失误,也会造成砼的强度不匀、产生的应力不均。 d )水泥急凝、需水性过大、安定性不合格等都极易造成混凝土“开裂”。
六、 302 加固型混凝土界面剂的工程应用
1 、影响混凝土界面粘结性的主要原因
在一定的环境条件下,混凝土结构材料有一定的使用寿命,因此需要定期地加固、修复甚至更换,近几年来,混凝土结构加固与修复的工程量在不断增加,加固修补混凝土的一般步骤是:混凝土基层处理、涂界面粘结剂、浇注新混凝土或加固修补材料、养护。新老混凝土之间的良好粘结是混凝土修补成功的关键所在,结构加固与修补的失效,大多数情况下都是由于新老混凝土之间局部或全部粘结失败。新老混凝土的粘结性能不仅与界面粘结剂的物理性质有关,粘结界面受力复杂,影响粘结的因素很多,主要包括:
( 1 )老混凝土基层状况及处理方法 旧基层的强度和完整性,粘结之前应打磨掉表面的薄弱浮浆层;基层的洁净程度,若混凝土表面有一层油污粘结就会很差;若基层的湿度过大,一些聚合物材料在潮湿条件下不能得到良好的固化。
( 2 )界面粘结剂的选择 如界面粘结剂的粘结强度偏低,无法承受所需用的荷载;若界面粘结剂的韧性不够,在振动环境容易引起脆性破坏。
( 3 )加固修补材料的选择 面层加固材料与基层混凝土两者的弹性模量相差悬殊,在一定的荷载条件下,膨胀或收缩引起的变形也会导致界面粘结力的丧失。
( 4 )新浇混凝土或加固修补材料的养护条件。
( 5 )加固修补结构所处的使用环境。
2 、 302 加固型混凝土界面剂的研究
根据《混凝土界面处理剂》 JC / T907 - 2002 的规定,通常“混凝土界面处理剂”是指“用于改善砂浆层与水泥混凝土、加气混凝土等材料基面粘结性的水泥基界面处理剂”,对于新老混凝土之间的界面也可参照该标准。在实际工程应用中,大多数的“混凝土界面处理剂”被用于改善水泥砂浆抹灰层与混凝土基层的粘结,因此,粘结强度只需满足最基本的要求,即拉伸粘结强度≥ 0.6MPa 。
混凝土结构加固是指对可靠性不足的承重结构、构件及其相关部分进行增强,使其具有足够的安全性和耐久性,常用的加固方法有增大截面加固法、局部置换混凝土加固法等,都需要在实施加固的原混凝土构件上重新浇注新的混凝土或修复材料,以提高其承载力和刚度,首先需要进行界面粘结增强处理,而普通的界面处理剂和水泥浆无法满足要求。
为满足混凝土加固的需要,达到面层混凝土与基层混凝土能够共同工作的目 的, 302 加固型混凝土界面剂的性能应达到在进行破坏试验时,粘结界面完好而基层破坏的效果。
|